Otherwise known as Shielded Metal Arc Welding (SMAW), STICK welding is a two-handed method, like TIG. STICK welding uses a metal filler rod, or stick, coated with flux. As the stick material melts in the heat, the flux coating also melts, creating both a gas and a liquid slag, which act to shield the weld from oxidation. As with FCAW, shield gas does not have to be dispensed during the welding process but the leftover slag leaves a mess requiring cleanup using a sander or solvents.
INTRODUCTION TO STICK WELDING
The history of STICK Welding can be traced back to 1800s. In 1800, British chemist and inventor Sir Humphry Davy developed an arc between two carbon electrodes using a battery.
Gas welding and cutting was introduced in the mid-1800s. It was in the 1880s that arc welding with the carbon arc and metal arc was developed.
In 1881, French electrical engineer Auguste De Meritens used the heat of an arc to join lead plates for storage batteries. His student Nikolai N. Benardos was awarded a patent for welding. In 1890, C.L. Coffin of Detroit was granted the first U.S. patent for an arc welding process using a metal electrode.
Around 1900, British inventor Strohmenger introduced a coated metal electrode. He used a thin coating of clay or lime and noticed that it provided a more stable arc.
During the period of 1907 to 1914, Oscar Kjellberg of Sweden came up with a coated electrode which looked like a stick.
Later on, pieces of iron wire dipped in thick mixtures of carbonates and silicates were used to make stick electrodes.

THE STICK WELDING PROCESS
STICK Welding is a process that uses a flux-coated electrode to form the weld. The electric current passes through the coated electrode or welding rod and arcs at the point of contact with the base metal. As the electrode begins to melt, the flux coating around it creates a cloud of gases that shields the molten metal and prevents it from oxidizing. This is why it also called shielded metal arc welding. The gas cloud settles on the pool of molten metal as it cools, and turns into slag which must be chipped off after welding is completed.
The STICK Welding process is quite simple and does not demand a great deal of specialized equipment.
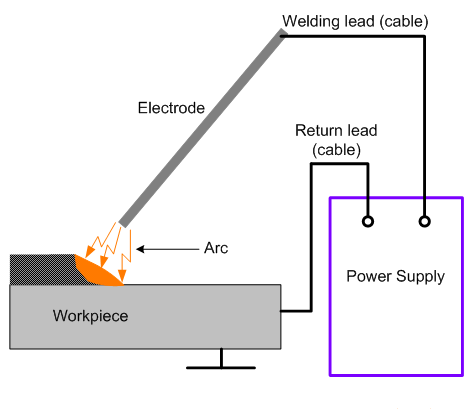
TIPS FOR BEGINNERS
Though STICK Welding is one of the most common forms of arc welding, it is a difficult process to learn. To be an effective STICK welder, one requires higher skill level and mastery of certain techniques. Here are three important things that a beginner needs to focus on.
Current Settings
The electrode you choose determines whether your machine requires DC positive, DC negative, or AC. Use the correct setting for your specific task. Electrode positive offers more penetration, while electrode negative gives better results for thinner metals. Select your amperage based on the electrode, welding position, and visual inspection of the finished weld. Follow manufacturer's recommendation for ideal amperage setting.
Length of Arc
Having the correct length of the arc is crucial for stick welding. Each electrode and application require a different length of arc not exceeding the diameter of the electrode. For example, a 0.125-inch 6010 electrode is held about 1/8 inch off the base material.
Angle of Travel
For welding in the flat, horizontal and overhead positions, use a 'drag' or 'backhand' technique. The electrode should be perpendicular to the weld joint. Tilt the electrode's tip at 5 to 15 degrees in the direction of its travel. For vertical welding that moves upward, use a 'push' or 'forehand' technique. Tilt the electrode away from the travel direction at 15 degrees.
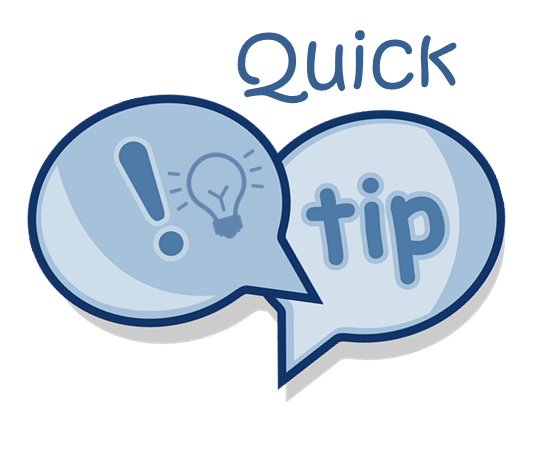
STICK WELDING PROS & CONS
Like any welding process, STICK welding has its pros and cons. Here are some of the most important ones:
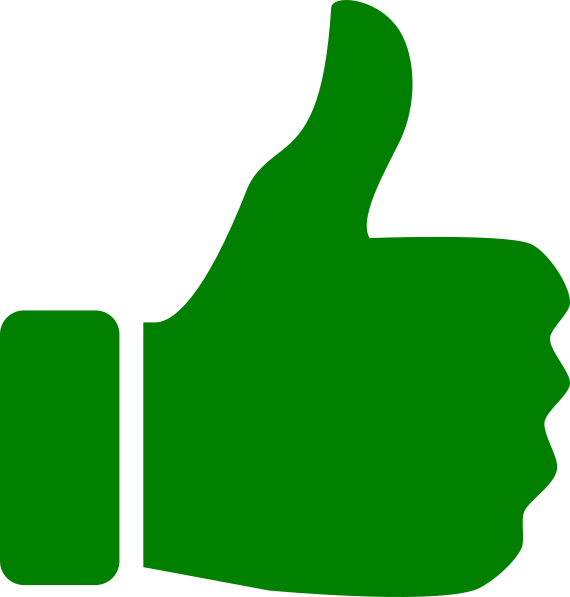
Pros:
• The equipment used for STICK welding is easy to use and inexpensive
• It does not require external shielding gas, thus saves money
• It can be carried out even when it's raining or windy
• It's easy to change electrodes for different metals
• Large range of metals and alloys can be welded easily
• Works well on painted or rusted surfaces

Cons:
• Operators need a high level of skill and experience
• It can be tough to work on certain thin metals
• Leaves slag to be chipped away after welding
• STICK welding is slow compared to other types of welding
• Electrodes must be replaced more frequently than in other types of welding
• Allows only short lengths of weld before a new electrode needs to be inserted
• It is not suitable for reactive metals such as titanium, zirconium, tantalum, and columbium
Safety is always the highest priority on a welding job site. A worker can always repair a piece of equipment or grind out a bad weld and re-weld a joint. However, a personal injury can be permanent. Hazards in welding can include hot metal burns, arc burns, hearing loss, dismemberment, and loss of eyesight.
All of these potential hazards should be taken very seriously. Which is why there are plenty of product offerings to choose from in the personal safety category. Before starting any welding operations, safety equipment should be purchased or borrowed then used.
RELATED PRODUCTS